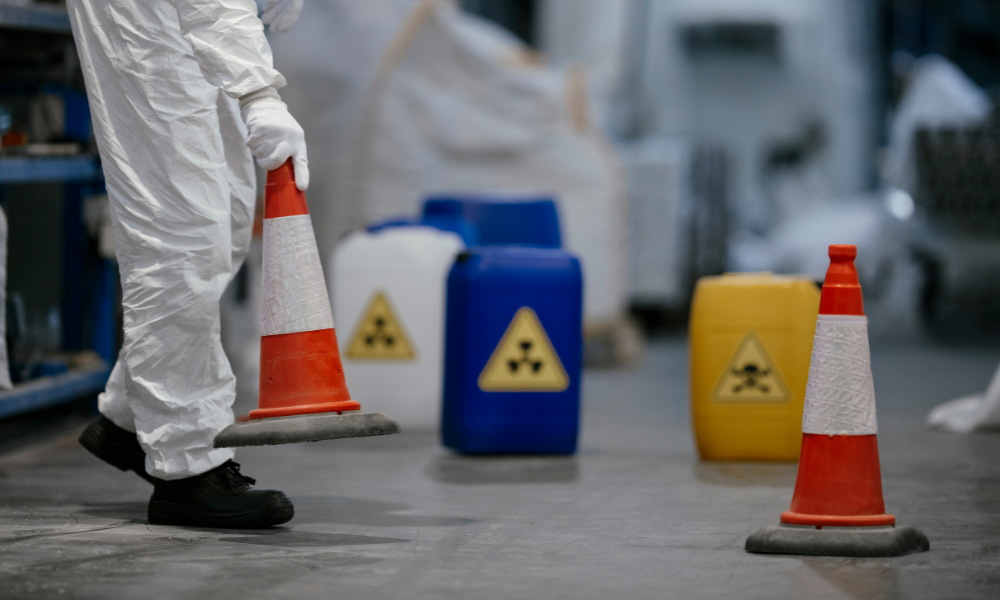
Lone worker situations are frequent in the workplace. In order to limit the number of incidents linked to these risky situations for employees, specific systems and measures need to be put in place. Whether it’s a risk analysis plan or the acquisition of a lone worker alarm system, safety measures adapted to lone working are both a moral and a legal obligation for employers, notably in Europe.
But over and above measures to improve response in the event of an incident, the introduction of accident prevention measures is essential. This not only protects employees’ health, but also avoids the legal and economic consequences that come with any accident.
Isolated workers face risks when carrying out their activities. These may be risks directly linked to the task they are executing, or risks linked to their isolation. However, preventive measures do exist to react before an accident occurs. This is what we propose to deal with in this article.
We will explore the following points:
-Risk situations for lone workers
-General principles of prevention in the workplace
-Accidents that can be avoided by using prevention equipment
-The advantages of Sysnav’s lone worker alarm system for prevention
Risk situations for lone workers
Definition of lone working
To fully understand the risks faced by a lone worker, and to differentiate them from the traditional risks to which all employees may be exposed, we need to look again at the definition of lone working.
In France, the highest Court (Cour de Cassation), in a ruling of November 25, 2008, states that an employee is in a lone working situation ‘if not within sight or hearing of others’.
An unusual or one-off activity, even one of short duration, may constitute a case of lone working. Employers must therefore take these situations into account in order to best adapt the measures they put in place to ensure the safety of employees who find themselves working alone.
This means highlighting all the possible scenarios in which an employee may find himself alone without being in the direct vicinity of another person to communicate his distress.
Although risks in the workplace do not only concern isolated workers, the risks are often greater for employees working in isolation. The absence of someone nearby limits the chances of being attended to quickly in an emergency, which can exacerbate the consequences of an accident.
Hazards for lone workers
The lone worker is confronted with numerous risks that can be classified into several categories:
-Physical risks, linked to the activity performed (handling dangerous products or heavy loads, for example),
-Medical risks, which are accentuated by working in isolation but are not directly linked to the worker’s activity,
-Risks related to the working environment (extreme heat, cold, presence of toxic products, etc.),
-Risks related to work organisation.
In addition to these various risks, lone workers are exposed to specific problems as a result of their isolation.
Isolation is in fact a factor that aggravates incidents. Delays in seeking medical attention can considerably increase the impact of an incident on a worker’s health. For example, in the event of a stroke (cardiovascular arrest), or a heart attack, delayed treatment can significantly worsen the consequences of the accident, or even lead to death.
In this respect, lone working calls for great vigilance on the part of employers, who must ensure that their employees do not find themselves in a situation of distress.
Lone workers are faced with several types of risks, linked not only to their isolation but also to the activities they carry out and their working environment. It is therefore essential to put in place appropriate safety measures to respond effectively to the issues specific to this situation.
General principles of prevention in the workplace
Incident prevention must be anticipated by the employer and EHS managers through a number of measures:
-Assessing the risks faced by workers
-Implementing preventive measures tailored to the risks identified
-Regular training of employees in risks and good prevention practices
-Adapting work organisation and introducing resources such as PPE (personal protective equipment) and verification protocols.
Analysis of occupational risks for companies is a legal requirement in the EU since the Council Directive of 12 June 1989 on the introduction of measures to encourage improvements in the safety and health of workers at work. Potential hazards to workers must be mapped out. The aim is to anticipate the different scenarios of risky or dangerous situations.
This mapping enables all the hazards for employees to be identified and the appropriate preventive measures to be put in place. The degree of seriousness of these risks must be assessed in a document. The document must also list all the preventive measures put in place to deal with the risks identified.
To ensure that the measures put in place are effective, the employer must ensure that his employees are regularly trained in prevention and that they are familiar with safety measures. Regular communication and training are therefore an essential aspect of prevention and safety within the organisation.
Avoiding accidents thanks to preventive equipment
Several types of frequent accidents can be anticipated and avoided using specific equipment. This is all the more important because the impact of an accident can be considerable, both legally and financially, if it causes a production stoppage.
What’s more, if an accident occurs on a site, it may be evidence of safety shortcomings on that site. Promoting accident prevention beyond the detection of actual incidents is strategic for companies.
Here we take a look at three typical situations where accidents can be avoided by using specific equipment.
How to prevent accidents linked to working at height ?
Working at height is a major issue, accounting for almost 10% of fatal accidents at work in France.
That’s why it is vital to install preventive equipment. Automatic detection of work at height can be particularly useful on certain industrial sites. This involves sending an automatic notification to the person in charge if the device worn by the operator detects that the height tolerated for safety reasons has been exceeded.
This alert can be sent directly to the worker to remind him that he must comply with the current protocol for working at height (appropriate protective equipment, safety harness, presence of a supervisor nearby, etc.). But it also allows the manager to be alerted so that he can send a supervisor to ensure that the employee is complying with safety standards.
Alerting the supervisor if the height allowed for an activity is exceeded therefore helps to anticipate and avoid an accident.
How to prevent accidents linked to entering a high-risk area ?
Some operations, such as maintenance shutdowns or certain types of work, require that employee access to certain areas be regulated because of the particular risks involved (risk of toxic products being released, presence of scaffolding with the risk of objects falling when work is being carried out, etc.).
Regulating access to an area for safety reasons is therefore necessary to guarantee the protection of employees. Real-time control of access to hazardous areas (or ‘geofencing’), via a geolocated lone worker protection system for example (such as Sysnav’s), means that employees can be warned that they are entering a hazardous area.
A safety manager can set access rights to these areas so that he or she is alerted if an unauthorised employee enters, thereby reducing the risk of accidents.
How to prevent gas leak accidents ?
Workers can be exposed to two types of risk from gases and vapours:
-The risk of intoxication: breathing and inhaling toxic gases (these gases are sometimes odourless)
-Anoxia: breathing in an atmosphere with too little oxygen (a situation found in confined spaces).
In both these cases, workers are exposed to fatal risks if they do not quickly evacuate the contaminated area or if they are not quickly attended to. Detecting gas leak occurences using fixed gas detectors helps to avoid these problems by sending alerts to workers as soon as they approach a contaminated area, or by alerting those in charge, who can then prohibit them from entering the areas in question. These fixed detectors complement individual portable gas detectors.
In this way, entry to an area with a gas alert can be prohibited automatically, enabling greater responsiveness in the event of an incident.
This type of system therefore requires the gas detectors and the worker to be precisely located in order to detect that they are entering a high-risk area and to trigger an alert.
A lone worker alarm system can help prevent accidents
At Sysnav, we are convinced that, in order to meet the challenges of employee safety, man-down systems should not be limited to the detection of actual incidents. In fact, the prevention and detection of dangerous situations are essential if we want to limit the risk of accidents in the workplace.
The aim is not only to protect a lone worker, but also to avoid the legal and economic consequences if an accident occurs. Not only can the employer be heavily penalised if a lone worker has an accident, but an accident can also lead to costly production stoppages for the company.
In this respect, the prevention of accidents in isolated work situations is strategic.
This is why the SYSNAV team has developed an innovative man-down device capable of :
– detecting and warning of high-risk situations, such as working at height and entering high-risk areas
– detecting actual incidents reliably (without false positives)
– alerting emergency teams
– locating endangered workers indoors and outdoors, and on the right floor, to ensure that they are attended to as quickly as possible, so as to limit the severity of incidents and comply with legal requirements.
Conclusion : lone worker alarm systems and prevention
Lone working involves risks that are accentuated by the worker’s isolation. Employers and EHS managers need to be extremely vigilant in these situations.
Indeed, over and above their moral duty, accidents in such circumstances can result in heavy criminal penalties for employers and significant costs for the company. In this respect, the choice of high-performance safety devices capable of preventing accidents as well as detecting them is strategic.
For more information about SYSNAV’s lone worker alarm solution, see Lone Worker Protection System