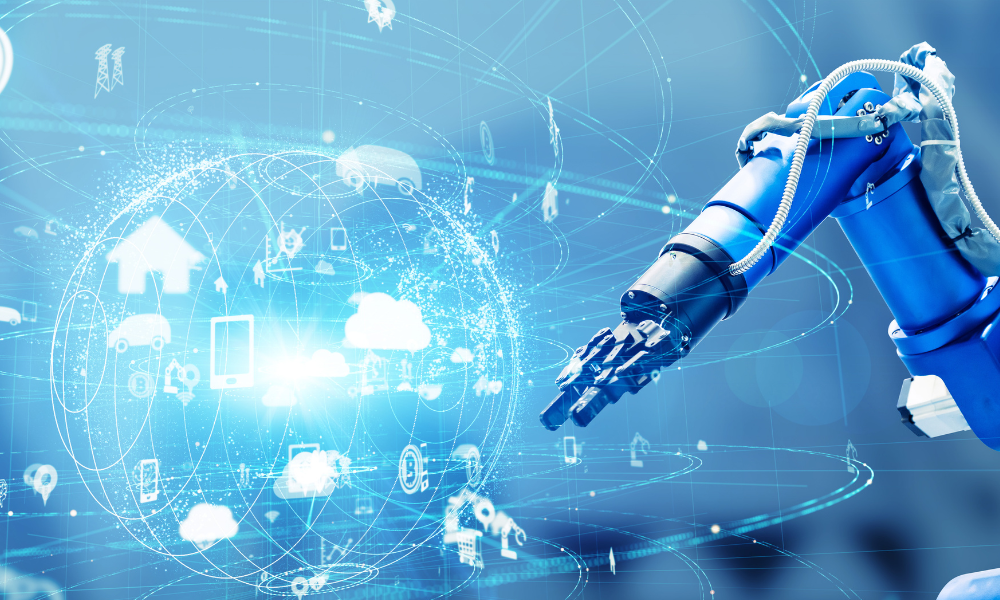
L’Industrie 4.0, considérée comme la “quatrième révolution industrielle”, marque une nouvelle étape dans l’histoire de la production. Cette révolution est marquée par l’idée d’introduire sur les sites industriels des technologies numériques. Elle promet ainsi d’optimiser et d’automatiser les usines. Qu’il s’agisse de l’internet des objets (IoT) ou encore de l’intelligence artificielle (IA), la mise en place de ces technologies nouvelles dans le monde industriel vise à rendre plus performants et plus fiables les processus de production.
Les enjeux de cette révolution sont non seulement économiques mais également sécuritaires et environnementaux. Il convient donc de se demander en quoi cette révolution peut faire évoluer les sites industriels et leurs performances mais il s’agit aussi de comprendre quels sont les champs d’application de ces technologies dans l’industrie et leurs perspectives.
Quelles sont les technologies de l’industrie 4.0 ?
L’industrie 4.0 repose sur un ensemble de technologies qui doivent à la fois permettre d’automatiser des tâches et d’améliorer la performance du système de production grâce à une adaptation en temps réel et une gestion des processus reposant sur l’analyse de données. Revenons plus en détails sur plusieurs technologies qui peuvent être mises en place dans l’industrie.
La mise en réseau/ connectivité
La mise en réseau (ou connectivité) est un des éléments essentiels de la « smart industry ». Il s’agit de rendre les entreprises industrielles capables de faire remonter en temps réel des informations afin d’adapter en permanence la production et pour optimiser leurs processus. La connexion entre les différents éléments de l’usine vise à permettre une amélioration de toutes les opérations du site : la production, les approvisionnements, la maintenance ou encore la gestion des stocks et la distribution. Il s’agit de faire remonter en permanence des informations pour coordonner les machines avec les décisions stratégiques et opérationnelles.
L’internet des objets (IoT)
La connectivité dont nous venons de parler est permise notamment grâce aux technologies IoT qui visent à mettre en réseau les machines grâce à des capteurs et différents réseaux de communication sans fil. Cela doit permettre une communication fluide entre les différents équipements du site. Ces éléments connectés sont capables de communiquer entre eux grâce à l’installation de contrôleurs logiques programmables (PLC) et de remonter leurs données aux Scada (systèmes de contrôle et d’acquisition de données).
Grâce à cette remontée permanente d’informations, les responsables d’un site industriel auront une meilleure compréhension des éléments et événements physiques du site. Ils seront donc capables de prendre des décisions stratégiques dans une perspective d’optimisation des processus et d’amélioration continue de la fabrication.
Les équipements connectés collectent et transmettent des données en temps réel, ce qui permet de mieux gérer la chaîne de production et d’approvisionnement. Grâce à l’IoT, les usines sont donc plus réactives face à une fluctuation de la demande.
L’IoT permet également une meilleure supervision des machines, offrant ainsi la possibilité de contrôler l’état des équipements, d’identifier les anomalies et d’anticiper les besoins en maintenance. Il s’agit donc, grâce à l’IoT, de récolter les données nécessaires au contrôle des machines et des besoins de production pour adapter les processus aux fluctuations éventuelles ou réduire les temps d’indisponibilité.
L’IoT promet donc de rendre les usines intelligentes en permettant grâce à la donnée d’adapter en permanence la production à la demande.
Cependant, cette mise en réseau des machines et cette connectivité impose un autre défi : celui du stockage et de la gestion des données.
Big Data et Analytique
Le volume de données générées par les usines augmente considérablement et ce d’autant plus avec la mise en place de technologies de l’industrie 4.0. Le Big Data fait référence à la gestion et au traitement de ces données en masse. Il s’agit de trier et d’analyser ces données pour obtenir des informations exploitables et pertinentes. L’utilisation de ces données permet aux entreprises d’optimiser leurs processus grâce à une prise de décisions éclairées par l’analyse de ces informations.
Il s’agit notamment d’adapter ses capacités de production en prévoyant les fluctuations de la demande ou de prévoir les cycles de maintenance des machines grâce à des capteurs ou encore d’améliorer sa supply chain grâce à une optimisation des flux et une anticipation des éventuels problèmes d’approvisionnement.
Cette compréhension fine de l’usine grâce à la donnée permet de réaliser des économies et de gagner en productivité.
Intelligence Artificielle
L’application de l’intelligence artificielle dans le monde industriel va permettre d’améliorer, d’optimiser, de prédire, et parfois automatiser, les processus de fabrication grâce à la valorisation des données récoltées. Elle va permettre notamment de traiter le volume d’informations recueillies, à la fois dans la partie production mais aussi au niveau des autres services de l’usine : la maintenance, la distribution, la partie commerciale ou encore la gestion du stockage.
De plus l’intelligence artificielle permettra aux systèmes de production de s’auto-optimiser en temps réel voire d’être automatisés. L’analyse de la donnée pourra en effet permettre d’identifier des schémas et prédire des résultats futurs, comme les pannes de machines, des besoins en maintenance ou encore des fluctuations au niveau de la demande. En automatisant ces processus de décisions, les entreprises vont augmenter leur efficacité et réduire les risques d’erreurs humaines et les temps d’arrêts liés à des défaillances imprévues.
Cloud Computing
Le cloud computing est essentiel pour la gestion des données dans l’Industrie 4.0. Il permet aux entreprises de stocker, gérer et traiter des données volumineuses sur des serveurs externalisés, plutôt que sur des systèmes internes coûteux et complexes. Grâce à cette infrastructure flexible, les entreprises peuvent centraliser la gestion de leurs données tout en facilitant la collaboration à distance. Le cloud permet également un accès rapide aux informations et donc d’améliorer la réactivité des processus de production et la coordination entre les différents sites industriels.
Réalité Augmentée (RA) et Réalité Virtuelle (RV)
La réalité augmentée et la réalité virtuelle sont des outils de l’Industrie 4.0 qui facilitent l’interaction entre les salariés et les systèmes industriels. La réalité augmentée permet notamment aux opérateurs de visualiser des informations en temps réel sur l’équipement ou les produits pendant les opérations de maintenance ou d’assemblage. Cela a pour but de faciliter les processus de production et de les améliorer grâce à un support numérique fiable. De plus cet outil permet de réduire les risques d’erreurs lors des opérations.
La réalité virtuelle peut être utilisée pour former les employés dans des environnements simulés ou pour tester des processus de production avant leur mise en place sur le site de production. Cette technologie permet donc de faciliter l’adoption d’un nouvel outil ou d’un nouveau processus grâce à une meilleure intégration des usages.
Localisation indoor et outdoor
Dans les environnements de production complexes et les grands sites industriels, la localisation des dispositifs et des outils est essentielle. En effet, une meilleure maitrise de la géographie du site et de la localisation des matériels en temps réel permet de faciliter les opérations et de garantir un meilleur contrôle de l’environnement.
A ce titre, les systèmes de géolocalisation performants, capables de localiser aussi bien en extérieur qu’en intérieur s’avèrent indispensables pour les directeurs de sites afin de suivre en temps réel le matériel et ainsi fluidifier les processus de maintenance et de production.
Cette capacité à localiser précisément des objets ou des personnes dans des espaces clos permet une gestion plus efficace des ressources, une optimisation des flux logistiques et une amélioration de la sécurité. Par exemple, dans un environnement de production, la géolocalisation indoor est nécessaire au mouvement des chariots ou des robots autonomes, garantissant que les matériaux et les pièces atteignent leur destination au bon moment.
De plus la localisation en temps réel et l’analyse des déplacements réalisés permet d’optimiser certaines opérations de production ou de maintenance en déterminant les parcours les plus pertinents et les moins coûteux en ressources.
Enfin l’intégration de systèmes de localisation dans certains dispositifs comme les DATI (dispositif d’alarme du travailleur isolé) ou dispositifs homme mort, permet de renforcer la sécurité des travailleurs. En effet, en intégrant une technologie de localisation précise dans les DATI, ces dispositifs peuvent non seulement alerter les équipes de secours une fois l’incident détecté, mais ils permettent également une prise en charge rapide grâce à une localisation précise du travailleur en détresse. A cet égard, des technologies de géolocalisation performantes en indoor/outdoor et en 3D seront particulièrement adaptées à ce cas d’usage.
Les promesses de l’industrie 4.0 : les applications concrètes
L’adoption des technologies de l’Industrie 4.0 vise à répondre aux défis de compétitivité, de sécurité et de durabilité des usines. Ses avantages sont donc nombreux et permettent d’améliorer le cadre de travail des salariés tout en augmentant les performances du site.
Flexibilité accrue et adaptation en temps réel
L’un des principaux objectifs de l’Industrie 4.0 est d’accroître la flexibilité des chaînes de production. Grâce à l’intégration des technologies numériques, les entreprises peuvent personnaliser les produits en fonction des besoins des clients, adapter la production en temps réel, et réagir plus rapidement aux fluctuations de la demande. Les usines deviennent ainsi plus réactives, capables de fabriquer de petites séries de produits personnalisés avec une efficacité s’approchant de celle des productions de masse.
Augmentation de la productivité
La mise en œuvre des technologies 4.0 permet aux entreprises d’augmenter leur productivité grâce à l’automatisation des processus ou une meilleure prévision des opérations de maintenance ce qui permet d’éviter des arrêts de production. En effet, les différentes technologies d’analyse et de traitement des données permettent de réduire les temps d’arrêt des machines et d’améliorer l’efficacité des équipements. Les systèmes de production sont capables de s’ajuster en temps réel pour maximiser leur rendement tout en minimisant les ressources utilisées.
Amélioration de la qualité
Les technologies de l’Industrie 4.0 permettent une surveillance en continu des processus de production, garantissant ainsi un contrôle de la qualité rigoureux. L’analyse des performances en temps réel permet de détecter plus rapidement rapidement les anomalies ou les défauts dans la chaîne de production. Les systèmes “intelligents” peuvent ainsi corriger les erreurs avant qu’elles n’affectent la qualité des produits finaux.
Réduction des coûts
L’automatisation des processus et la gestion optimisée des ressources permettent aux entreprises de réduire leurs coûts de fonctionnement notamment en optimisant la consommation en énergie du site. La maintenance prédictive permet de prévoir les pannes et d’éviter les interruptions coûteuses. De plus, le cloud computing permet de réduire les investissements en infrastructures informatiques et les prévisions de fluctuations de la demande permettent de mieux gérer les stocks et éviter le gaspillage de ressources.
Durabilité et environnement
L’Industrie 4.0 permet de réduire considérablement le gâchis ainsi que la consommation d’énergie grâce à l’optimisation des processus de production. A ce titre l’industrie 4.0 peut jouer un rôle important dans la transition énergétique et permettre aux usines d’être plus vertueuses sur le plan environnemental tout en faisant des économies significatives grâce à la réduction des pertes et une gestion optimisée de l’énergie.
L’optimisation des stocks et des ressources permet de limiter les déchets et donc de réduire de facto leur empreinte carbone. De plus, des processus plus efficaces et automatisés permettent de réduire la consommation d’énergie, et une meilleure gestion des fluctuations de la demande limite la surproduction. Les technologies intelligentes favorisent également une gestion plus durable des chaînes d’approvisionnement, notamment en réduisant les distances de transport.
Sécurité
L’industrie 4.0 transforme la sécurité au travail en intégrant des technologies avancées sur les sites industriels où les risques d’accidents sont élevés. Grâce aux capteurs connectés, les employeurs peuvent surveiller en temps réel les conditions de travail, anticiper les risques et intervenir plus rapidement en cas d’incident.
Les dispositifs de Protection du Travailleur Isolé (PTI) ou DATI, par exemple, couplés à la géolocalisation et aux systèmes d’alertes automatiques, permettent de mieux protéger les employés exposés aux dangers. L’automatisation et la robotique réduisent également les tâches à risque, contribuant ainsi à un environnement plus sûr et plus efficace. Ces innovations permettent la prévention des accidents et aux employeurs d’être en conformité sur le plan légal.
Remettre l’humain au centre avec l’industrie 5.0
L’industrie 4.0 ne cesse d’évoluer et offre de véritables perspectives pour l’avenir de l’industrie manufacturière. La montée en puissance de l’IA, du cloud et des technologies comme l’IoT ou la géolocalisation indoor, promet de rendre les processus de production plus intelligents, plus autonomes, plus respectueux de l’environnement et plus en phase avec les problématiques de sécurité des travailleurs. Le développement des usines intelligentes, interconnectées et flexibles, est au cœur de cette révolution.
Mais au-delà de répondre à la promesse d’une industrie capable de faire face aux enjeux environnementaux et technologiques, il est fondamental de garder à l’esprit les aspects sociaux d’une telle révolution. C’est d’ailleurs ce qui a poussé la Direction générale de la recherche de la Commission européenne à publier en 2023 une étude sur « l’industrie 5.0 ».
L’idée forte de cette étude est de réinsister sur l’aspect humain dans les évolutions industrielles à venir afin de faire en sorte que le nouveau modèle d’industrie mette les employés au centre de ses priorités. Il s’agit en effet de s’assurer que ce sera la machine qui s’adaptera au salarié et non la technologie qui s’imposera à lui. C’est en effet une des clés des prochains gains de productivité et d’adaptabilité de l’activité industrielle.
Plus d’informations sur nos solutions d’industrie 4.0 sur la page Localisation et mesure pour la performance industrielle
Les sujets qui pourraient vous intéresser :
La localisation de précision au service de l’industrie 4.0