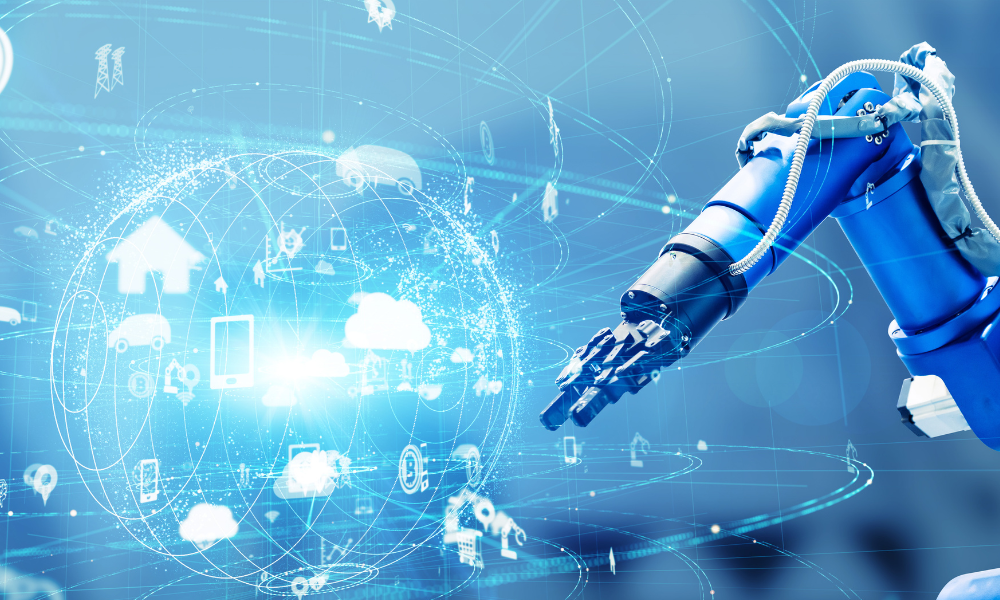
Industry 4.0, often referred to as the “fourth industrial revolution,” represents a new chapter in industrial production history. This revolution is characterized by the integration of digital technologies into industrial environments, aiming to optimize and automate factories. Whether through the Internet of Things (IoT) or artificial intelligence (AI), the implementation of these technologies in the industrial world seeks to enhance both the efficiency and reliability of production processes.
Implications of this revolution are not only economic but also concern security and environmental sustainability. This prompts questions on how the industry 4.0 revolution will transform industrial sites and their performance, while also exploring the wider application potential of these technologies within the industry.
What are industry 4.0 technologies?
Industry 4.0 relies on a suite of technologies designed to automate tasks and enhance production systems through real-time adaptation and process management based on data analysis. Let’s take a closer look at several key technologies that are being implemented in the industry.
Networking and connectivity
Networking, or connectivity, is one of the fundamental components of the “smart industry.” This technology allows industrial companies to exploit real-time information, facilitating continuous production adjustments and process optimization. Connecting various elements of the factory enables improvements across site operations, including production, supply chain, maintenance, stock management, and distribution. The goal is to have constant upstream data flow, coordinating production machines with strategic and operational decisions.
Internet of Things (IoT)
Connectivity, as previously discussed, is largely enabled by IoT technologies, which interconnect machines via sensors and wireless communication networks, ensuring seamless communication between equipment. These connected elements can communicate autonomously through programmable logic controllers (PLCs) and transmit data to SCADA (Supervisory Control and Data Acquisition) systems.
With this constant data feedback, industrial site managers gain a clearer understanding of on-site physical elements and events, enabling strategic decision-making for process optimization and continuous improvement. IoT allows real-time data collection, enhancing production and supply chain management and enabling plants to respond more effectively to demand fluctuations.
Additionally, IoT improves machine monitoring, enabling equipment status control, anomaly detection, and maintenance forecasting. Thus, IoT helps gather essential data to manage machines and production needs, adapting processes to demand fluctuations and reducing downtime.
Big data and analytics
The volume of data generated by factories has increased significantly, particularly with the implementation of Industry 4.0 technologies. Big Data refers to the management and processing of these vast data sets, sorting and analyzing them to obtain relevant, actionable insights. Using this data allows companies to optimize their processes through data-informed decision-making.
For instance, it enables companies to adjust production capacities based on demand fluctuations, forecast maintenance cycles through sensors, or improve supply chain efficiency by optimizing flows and anticipating supply challenges. This fine-grained understanding of the factory, enabled by data, translates into cost savings and productivity gains.
Artificial intelligence
AI in the industrial sector can improve, optimize, predict, and, in some cases, automate manufacturing processes by leveraging collected data. It aids in handling large volumes of information, not only in production but also in other plant areas like maintenance, distribution, sales, and inventory management.
AI allows production systems to self-optimize in real time and even enables automation. Data analysis can identify patterns and predict future outcomes, such as machine breakdowns, maintenance needs, or demand fluctuations. By automating decision-making processes, companies enhance efficiency, reduce human error risks, and minimize downtime caused by unforeseen failures.
Cloud computing
Cloud computing is essential for data management in Industry 4.0, allowing companies to store, manage, and process vast amounts of data on externally managed servers rather than costly, complex in-house systems. This flexible infrastructure enables centralized data management while facilitating remote collaboration. The cloud also provides rapid access to information, improving production processes’ responsiveness and coordination across industrial sites.
Augmented reality (AR) and virtual reality (VR)
AR and VR are Industry 4.0 tools that streamline the interaction between employees and industrial systems. AR allows operators to visualize real-time information on equipment or products during maintenance or assembly, facilitating and enhancing production processes with reliable digital support. Additionally, this tool reduces error risks during operations.
VR, on the other hand, can train employees in simulated environments or test production processes before implementation. This technology aids the integration of new tools or processes, making adoption smoother.
Indoor and outdoor localization
In complex production environments and large industrial sites, tracking devices and tools is essential. Real-time geographic awareness of the site and equipment improves operational flow and environmental control.
High-performance localization systems, effective both indoors and outdoors, are crucial for site managers to monitor mobile assets in real-time, enhancing maintenance and production flows.
This ability to pinpoint the precise location of objects or people in confined spaces means that resources can be managed more efficiently, logistics flows optimised and safety improved. For example, in a production environment, indoor localization is necessary for the movement of forklift trucks or autonomous robots, ensuring that materials and parts reach their destination at the right time.
In addition, real-time location and analysis of movements enables certain production or maintenance operations to be optimised by determining the most appropriate and least resource-intensive routes.
Furthermore, integrating localization systems into devices like Lone Worker Alarm Devices enhances worker safety. Equipped with precise indoor location technology, Lone Worker Alarm Devices can alert rescue teams when incidents are detected, enabling swift responses due to accurate worker location data, and eventually shortening work interruptions. Robust indoor/outdoor 3D geolocation systems are especially well-suited to such use cases.
The Promises of Industry 4.0: Practical Applications
Adopting Industry 4.0 technologies addresses competitiveness, safety, and sustainability challenges for factories, offering numerous benefits that improve employees’ working conditions while boosting site performance.
Enhanced flexibility and real-time adaptation
One of the main objectives of Industry 4.0 is to increase production line flexibility. Through digital integration, companies can customize production batches based on client needs, adjust production in real-time, and react faster to demand shifts. Factories become more responsive and able to manufacture smaller, customized product series with mass-production efficiency.
Increased productivity
Implementing 4.0 technologies enables companies to boost productivity by automating processes and forecasting maintenance to avoid production stops. Data analytics and processing technologies reduce production downtime and improve equipment efficiency. Production systems can adjust in real-time to maximize output while minimizing resource use.
Improved quality
Industry 4.0 technologies enable continuous production monitoring, ensuring rigorous quality control. Real-time performance analysis allows for faster anomaly or defect detection in the production chain, and “intelligent” systems can correct errors before they affect the final product quality.
Cost reduction
Automating processes and optimizing resource management allows companies to reduce operating costs, especially by optimizing energy consumption. Predictive maintenance prevents breakdowns, avoiding costly interruptions. Additionally, cloud computing reduces IT infrastructure investments, and demand forecasting helps manage inventory, minimizing resource waste.
Sustainability and environmental impact
Industry 4.0 reduces waste and energy consumption through production process optimization. It plays a significant role in the energy transition, making factories more environmentally friendly while achieving significant savings by reducing waste and managing energy more efficiently.
Optimizing inventory and resources minimizes waste and carbon footprints. More efficient, automated processes reduce energy consumption, while better demand management limits overproduction. Smart technologies also promote a more sustainable supply chain, reducing transportation distances.
Safety
Industry 4.0 enhances workplace safety by integrating advanced technologies into industrial sites with high accident risks. Connected sensors allow employers to monitor working conditions in real-time, anticipate risks, and respond more swiftly to incidents.
Lone Worker Alarm Devices or Man Down Devices, combined with geolocation and automatic alert systems, improve employee safety. Automation and robotics also reduce hazardous tasks, contributing to a safer and more efficient work environment, preventing accidents, and ensuring legal compliance for employers.
Toward Human-Centric Manufacturing with Industry 5.0
Industry 4.0 continues to evolve, offering genuine prospects for the future of manufacturing. The rise of AI, cloud computing, IoT, and indoor geolocation promises smarter, more autonomous, environmentally-friendly production processes that address worker safety issues. Developing intelligent, interconnected, and flexible factories lies at the heart of this revolution.
However, beyond meeting environmental and technological demands, it’s crucial to remember the social aspects of this revolution. This is the guiding principle behind the European Commission’s 2023 study on “Industry 5.0.”
The key idea in this study emphasizes putting people at the heart of future industrial advancements, ensuring that new industry models prioritize employees. It’s about ensuring that machines adapt to employees rather than imposing technology on them—a crucial aspect for future productivity gains and industrial adaptability.
For more information on our Industry 4.0 solutions, please visit the Industrial Sites page.
Topics you may be interested in:
Precision Localization for Industry 4.0 (upcoming)